1 10
1 10
PepsiCo's Frito-Lay Modesto has been a part of California's Stanislaus County community for 21 years. The more than 340,000-sq.-ft. building sits on approximately 80 acres of land. Frito-Lay Modesto produces some of America’s favorite snacks including Lay’s and Ruffles potato chips, Sunchips, Tostitos tortilla chips, Doritos tortilla chips and Cheetos cheese-flavored snacks.
In 2011, the facility was California's first food manufacturing site to be awarded LEED Gold EB (existing building) certification. Frito-Lay North America now has eight certified LEED Gold EB buildings across the country, with manufacturing sites in Casa Grande, Ariz., Topeka, Kan., Perry, Ga., Beloit, Wis., Jonesboro, Ark., and Killingly, Conn., and its Plano, Texas-based headquarters.
The Frito-Lay Modesto facility reduced its natural gas consumption by 25 percent per pound of product and its electricity use by 24 percent per pound of product since 1999 by installing new technologies such as the 1-megawatt photovoltaic solar system, which generates nearly 25 percent of the facility’s electrical requirements when in operation, high-efficiency lighting throughout the plant and a thermal solar system which generates steam to help cook chips. These and other initiatives greatly reduce the facility’s emissions of carbon dioxide and nitrous oxide.
The facility reduced its water consumption by nearly 36 percent per pound of product since 1999 by implementing technologies that reduce water used in its corn cooking and potato-chip processing. The facility also implemented automatic sinks and hand-washing stations with low-flow fixtures.
More than 98 percent of the Modesto facility’s solid waste is diverted from landfills. The site achieved this milestone through many initiatives, including an employee-led recycling program, reusing cardboard shipping boxes multiple times, and allocating waste product for use in animal feed.
General Mills opened the largest LEED Gold certified facility of its kind in North America at a special ceremony in Fort Wayne, Ind., in 2012. The facility is the largest warehouse and distribution center project in North America to achieve LEED Gold Certification and the third largest in the world.
Its sustainable features include several retention ponds that hold storm water that comes from the roof and paved areas. This water is used to irrigate the landscaping around the property. Inside, the building has low-flow plumbing that reduces water use by 33 percent. There are also a number of elements in place designed to save energy such as energy- efficient light fixtures, occupant sensors, high-efficiency HVAC systems, roof mounted up-blast exhaust fans and wall louvers. These features help make the facility 45 percent more energy efficient than the baseline model for industrial buildings.
In addition, the construction of the facility followed several environmentally conscious building practices. Eighty-five percent of the construction waste, totaling more than 596 tons of material, was diverted from landfills by sorting the materials and sending them to the appropriate recycling centers for reuse on other products. Forty-four percent of the construction materials were extracted, processed or manufactured within 500 miles of the project site.
General Mills' customer service facility in Fort Wayne was the company's fifth building to attain LEED certification since 2010.
Boeing's LEED-Gold-certified 1.2-million-sq.-ft. facility, located on a 265-acre campus in North Charleston, S.C., is the third of its type in the world to assemble 787s. In about a year from now, a larger version of the 787 Dreamliner should be rolling off the plant's production line. By using renewable energy, attaining LEED certification and recycling 3,000 tons of waste each year, it is setting an example for future factories. In April 2011 Boeing and South Carolina Electric and Gas partnered to ensure renewable energy capacity for the entire Boeing South Carolina site. The site is the first within Boeing to commit to 100 percent renewable energy. A major component of this partnership is the installation of thin-film solar laminate panels on the roof of the new 787 Final Assembly building, providing approximately up to 2.6 megawatts of electrical power for the site, enough to power 250 homes. The remainder of the renewable energy comes from SCE&G biomass energy generation facilities in South Carolina. Boeing South Carolina is also a zero-waste -site, meaning that no waste generated at the site is sent to landfill.
Waste material is recycled, reused, repurposed or sent to energy recovery facilities.
The installation of thin-film solar laminate panels on the Boeing South Carolina Final Assembly building was the largest rooftop solar installation in South Carolina and the Southeast by production capacity at the time of the April 2011 announcement. This was also the sixth-largest rooftop thin-film solar laminate installation in the United States by production capacity at the time. The solar installation is capable of producing 2.6 megawatts of energy at peak capacity at a single point in time, and up to 20 percent of the site’s total energy needs. The sum of energy produced over a year is 3,500 megawatt hours, equivalent to the annual usage of 250 SCE&G residential homes. The peak energy produced by the solar installation could instantly light 200,000 energy-efficient light bulbs. Approximately 10 acres of thin-film laminate panels (18,095 individual panels) are installed on the Final Assembly building roof. The total square footage of the solar generation system is equal to approximately eight football fields.
Johnson Controls' Horizon Business Park certified as LEED BD+C for New Construction in 2009 and as LEED Silver in 2011. In 2012, Johnson Controls was named No. 5 among the “100 Best Corporate Citizens” in the United States by Corporate Responsibility magazine. In addition, it was ranked No. 3 on the Maplecroft Climate Innovation Index for its carbon disclosure practices, and as one of the “World’s Most Ethical Companies” for the sixth consecutive year by Ethisphere Magazine. The company is among a group of select companies recognized on a number of social investor indices, including the Dow Jones Sustainability World and North America indices and the FTSE4Good Index.
Johnson Controls Building Efficiency delivers products, services and solutions that increase energy efficiency and lower operating costs in buildings for more than one million customers. Operating from nearly 700 branch offices in more than 150 countries, we are a leading provider of equipment, controls and services for heating, ventilating, air conditioning, refrigeration and security systems. Each year, Johnson Controls is involved in more than 100 renewable energy projects including solar, wind and geothermal technologies. Its solutions have reduced customers’ carbon dioxide emissions by more than 19 million metric tons and generated savings of $7.5 billion since 2000.
UT Electronic Controls, a division of Carrier Corp., is the largest maker of HVAC electronic controls in the United States and in 2011 was the first electronics manufacturing facility to earn received LEED Gold EB:O+M certification (for existing buildings operation and maintenance). In 2009, the facility had received LEED EB certification (for existing buildings).
UTEC reduced energy consumption by 29 percent compared to similar facilities, decreased water consumption from plumbing fixtures by 30 percent compared to the LEED baseline and lowered single-occupant vehicle trips 10 percent by promoting employees carpooling. UTEC also added a cooling tower with automated controls to help reduce water usage.
In 1988, Carrier was one of the first companies to set energy reduction goals for its factories, and is a founding member of the USGBC chapters in the United States, Argentina, India, China, Singapore and France. The company's Monterrey, Mexico, commercial plant was the first industrial facility in the global HVAC industry to be LEED Gold certified.
In 2008, Intel's Ocotillo campus, which is the company's second-largest site globally, became one of the first campuses of semiconductor manufacturing to be certified as LEED EB:O&M (existing building operation and maintenance). The 682-acre campus in Chandler, Ariz., is complex, featuring almost 4 million sq. ft. of conditioned space consisting of three wafer fabrication plants, two central utility plants (housing chillers, boilers, waste and wastewater treatment) and one emergency generator building. Intel pursued LEED certification after research determined that its current method of designing, building and operating met LEED criteria without major capital investments. During a three-year LEED performance period, Intel achieved $1.58 million in cost savings.
More than half of the electricity at Siemens’ light rail manufacturing plant in Sacramento comes from solar-power generated on site. Siemens is ready to expand this facility so that high-speed rail can be built in America.
For the 10th consecutive year, Siemens has been listed on the Dow Jones Sustainability Index and is the top company in the Diversified Industrials Sector. The Sacramento plant is solar-powered, with more than half of the electricity used by the facility being generated by solar panels that the company installed. Currently, the plant is expanding its capacity and by the end of 2014, will generate about 90 percent of its power needs.
Siemens employs a dry-cut welding process to eliminate water waste. This special dry-cut welding technology requires no water disposal, and reduces the impact on the environment and results in a superior product. Siemens trains its own technicians at its facility on this process.
The plant has cut volatile organic compound waste by more than 50 percent while at the same time increasing production by more than 200 percent over the last three years. Up to 82 percent of all the non-food/wet waste materials from the facility is sent for sorting and recycling. All emptied 55-gallon drums on the property are either sent back to the supplier for reuse or recycled for scrap metal.
Volkswagon's Chattanooga manufacturing plant received LEED Platinum certification in 2012--the only one of its type in the global automotive manufacturing industry. That year the company launched its "Think Blue" program to reach the highest level of environmental protection and corporate social responsibility possible. Some of the plant's green highlights are:
- Certification of the paint shop building. The sustainably-designed building saves more than 50 million gallons of water annually. Previous assembly plants excluded their paint shop in the LEED certification process.
- Salvaging or recycling nearly 78 percent (4,602 tons) of construction and demolition waste.
- 48 percent of building materials manufactured using recycled materials.
- 58 percent reduction in potable water through low-flow water closets and urinals and rainwater harvesting from its roof, collected for use in the sanitary waste system. Together these measures save 1.7 million gallons of potable water each year. Low-flow showers and restrooms and kitchens faucets save a further 3 million gallons per year.
- Reflection roofing material installation on 100 percent of the roof area of the building to reflect heat, lower cooling costs and save energy.
- Exterior lights providing only minimum lighting required for safety, thus eliminating light pollution and avoiding adverse effects on the surrounding wooded environment.
- Installation of bike racks for visits and employees and preferred parking for low-emitting and fuel-efficient vehicles and carpool vehicles.
In 2011, ConAgra Foods Lamb Weston's Delhi, La., processing facility became the first frozen food manufacturing plant worldwide to earn LEED Platinum certification. The design, construction and operations at the Delhi processing facility were developed with sustainability in mind. The plant primarily processes sweet potatoes from Louisiana and the surrounding states, and was built from the ground up using the newest and best processing and packaging technologies. The plant's state-of-the-art equipment was designed to process sweet potatoes in the most efficient and environmentally-responsible way. The plant will eventually convert fresh sweet potatoes into many different consumer and restaurant products prepared from frozen. Efficient operations mean more efficient use of natural resources within the community, including energy and water. Employees also benefit from the green building design; it is climate-controlled throughout to enhance productivity, safety and comfort. The building's highlights include:
- The entire plant is climate controlled to increase worker productivity, safety and comfort. Climate control in such a hot, humid environment cuts condensation buildup and water on the floors, reducing slip and fall and hazards.
- Low-VOC carpeting, cleaning products and paints used in the interior of the plant to reduce occupant exposure to airborne pollutants.
- Energy-saving equipment saves 40 percent of the annual energy consumed at a comparable plant. By identifying and recovering potential wasted energy within the building systems and processes, energy demand is greatly reduced.
- Biogas, produced by treating process waste water, is piped back to the plant boilers to produce steam. This process is expected to offset approximately 20 percent of the annual natural gas demand of the plant, and prevents methane from entering the atmosphere.
- More than 100 acres of the property are maintained as open space, including protected wetland areas, ponds and restored native vegetation. *Water is conserved outside the building by landscaping with native plant species that require no irrigation once established.
- Priority parking is given to low-emission, fuel efficient vehicles.
The 1.82 million-sq.-ft. SKECHERS facility certified in 2013 as the largest LEED-certified building in the United States. It opened for operation in 2011. Not only is the building sustainable, but the new state-of-the-art automated design allows the company to ship 100 million pairs of shoes annually, effectively growing the business with reduced impact to the environment. In addition to the warehouse operations, which can process 18,000 to 20,000 pairs of shoes for distribution in one hour, the structure includes 20,000 sq. ft. of office space and a SKECHERS retail store.
Highlights include:
- 280,000 sq. ft. of solar-power generation systems on the roof.
- Lighting that operates as needed, regulated by motion sensors and powered in part by solar panels.
- A warehouse ventilation system that utilizes outside air drawn through louvers facing the prevailing winds, plus energy-efficient heating and cooling systems.
- A solar reflective white “cool roof” and light-colored on-site pavement to reduce heat and global warming.
- Water-efficient and drought-tolerant landscaping that reduces irrigation by 50 percent.
- A water pollution prevention program that captures and treats storm water runoff from 90 percent of annual rainfall.
- Low-emitting paints, coatings, glues, and sealants that comply with LEED standards were used during construction.
- Recycled and regional building materials were sourced within 500 miles of the construction site. The majority of on-site construction waste materials were recycled as well.
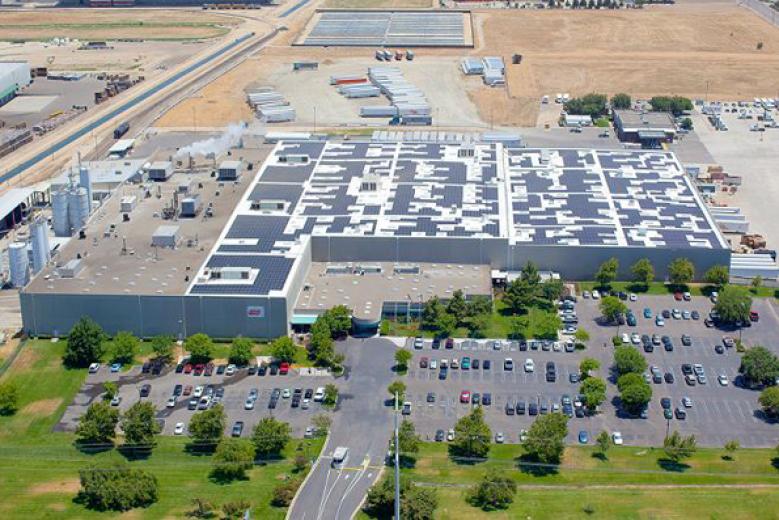